Merced College has started providing 3D-printed face shields and mask components for local area health care workers at Mercy Medical Center Merced.
Merced College 3D prints face shields to help meet demand at local hospital
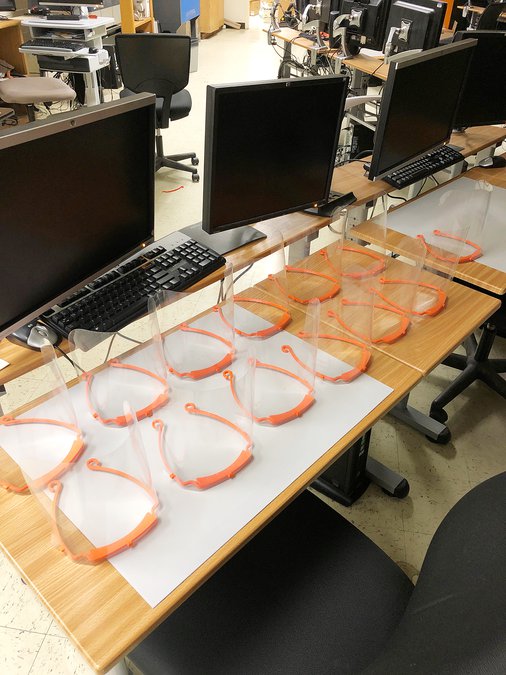
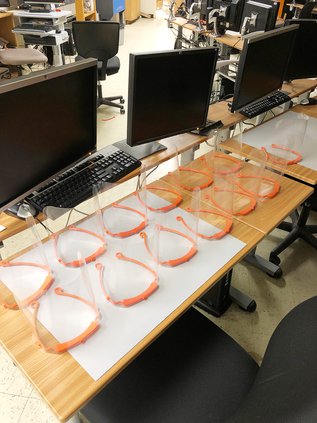